Monitoring Mud Properties on the Rig
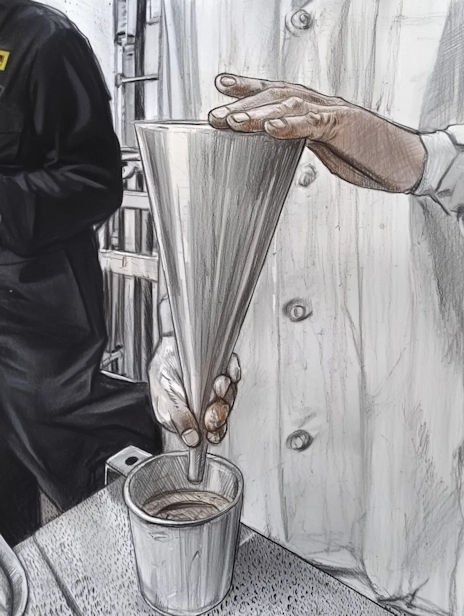
Mud properties are essential parameters monitored on an oil and gas drilling rig to ensure proper well control, prevent formation damage, and optimize the drilling process. Drilling mud (or drilling fluid) serves several crucial functions, including cooling and lubricating the drill bit, stabilizing the wellbore, controlling pressure, transmitting signals from downhole tools to the surface, and carrying drill cuttings to the surface. Monitoring and interpreting the properties of drilling mud is vital for maintaining safe and efficient operations.
Key Mud Properties Monitored on a Drilling Rig:
Density (Mud Weight):
- What it is: Density is the weight of the drilling mud per unit volume, typically measured in pounds per gallon (ppg), kilograms per cubic meter (kg/m3) or kilograms per
liter (kg/L). - Why mud weight is important:
- The primary function of mud weight is to exert hydrostatic pressure on the wellbore to prevent the influx of formation fluids (such as gas or oil), which can lead to a blowout.
- Mud weight must be carefully controlled to balance the formation pressure. If it is too low, it may not provide enough pressure to control formation fluids. If it is too high, it could cause formation damage or induce fractures.
- How to interpret the mud weight:
- Consequence of being too high: May result in fracturing the formation and losing circulation.
- Consequence of being too low: May lead to a kick (influx of formation fluids) or even a blowout.
- Knowing the optimal range: The ideal mud weight depends upon knowing the specific well conditions, formation strengths, formation pressures, and other formation characteristics.
Viscosity:
- What it is: Viscosity measures the resistance of a fluid (the drilling mud) to flow,
typically measured using a rotational type viscometer. The most common viscosity
measurements made at the rig are plastic viscosity (PV) and yield point (YP). - Why it is important:
- Viscosity influences the mud’s ability to carry cuttings to the surface. High viscosity helps suspend drill cuttings and prevent them from settling.
- A balance of viscosity is needed to ensure efficient hole cleaning without causing excessive pressure buildups in the wellbore.
- How to interpret it:
- Plastic viscosity: A high plastic viscosity indicates thicker mud caused by the presence of excessive colloidal solids, which can cause drag and results in a slower penetration rate. A low plastic viscosity can lead a faster drilling rate but less efficient hole cleaning.
- Yield point: A higher yield point means the mud can suspend cuttings more effectively, which is crucial for maintaining wellbore stability, carrying cuttings to surface, and preventing bridging.
- Optimal range: The viscosity should be adjusted depending on the size and depth of the hole, drillstring size, penetration rate, size and shape of cuttings, and the type of formation being drilled.
- What it is: Viscosity measures the resistance of a fluid (the drilling mud) to flow,
Filtration Control (API Fluid Loss):
- What it is: Fluid loss (water loss) refers to the amount of liquid that leaks from the drilling mud into the formation, loosely estimated by using API filter press and reported in mL/30 minutes at 100 psi pressure differential.
- Why it is important:
- A high fluid loss can cause many formations to become unstable, leading to wellbore damage and impaired oil and gas production. Low fluid loss muds are preferred to prevent wellbore damage and the loss of valuable drilling fluids into the formation.
- Excessive filtration can also result in formation damage causing sloughing shales, resulting in poor hole cleaning, which impacts the ability to control well pressure.
- How to interpret it:
- High fluid loss: Indicates potential for loss of mud filtrate to formation, causing instability and possible damage to the wellbore.
- Low fluid loss: Indicates better control over formation pressures and reduces the risk of formation damage.
- Optimal range: Depends on the type of formation being drilled, but lower fluid loss is generally preferred for stability and efficient hole cleaning. The optimal range is often a compromise between cost and effectiveness in non-critical wells and will vary at different stages of drilling.
- How to interpret it:
pH Level:
- What it is: pH measures the acidity or alkalinity of the drilling mud. In a typical well it generally ranges from about 4 (acidic) to 12 (basic), with 7 being neutral.
- Why it is important:
- The pH of the mud affects the effectiveness of chemical additives and the prevention of corrosion of the drillstring.
- It is particularly important for preventing the breakdown of certain drilling fluid components and for maintaining the stability of the mud.
- How to interpret it:
- Low pH (acidic): May cause corrosion of metal components (such as pipes) and affect the performance of mud additives.
- High pH (alkaline): Can decrease the effectiveness of some additives.
- Optimal range: A pH level between 8.5 and 10.5 is often ideal for most drilling muds:
however, there may be exceptions for specialized types of muds.
Alkalinity (or Alkaline Reserve):
- What it is: Alkalinity measures the ability of the mud to resist changes in pH due to chemical reactions. It is measured using titration methods.
- Why it is important:
- Alkalinity helps to stabilize the mud and prevent pH fluctuations, especially when
drilling through formations that may release acid gases like CO? or H?S.
- Alkalinity helps to stabilize the mud and prevent pH fluctuations, especially when
- How to interpret it:
- Too low alkalinity: The mud is more likely to experience pH drop, leading to corrosion and instability.
- Too high alkalinity: May cause reduced mud performance or the precipitation of certain chemicals.
- Optimal range: Alkalinity should be maintained within a specific range to keep pH stable and prevent excessive chemical breakdown.
Gel Strength:
- What it is: Gel strength refers to the ability of the mud to suspend cuttings when circulation is stopped, typically measured in pounds per 100 square feet (lb/100ft²).
- Why it is important:
- Gel strength indicates the mud’s ability to suspend cuttings during periods of non-circulation, such as when the drill string is pulled out of the hole.
- High gel strength can help prevent cuttings from settling, reducing the risk of stuck pipe.
- How to interpret it:
- High gel strength: Indicates that the mud is capable of suspending cuttings effectively when circulation stops. However, excessive gel strength can lead to difficulty in breaking circulation and an undesirable increase in pump pressures. These higher transient pressures can pose a well control hazard.
- Low gel strength: Indicates that the mud may not effectively suspend cuttings, which could lead to problems when circulation is resumed.
- Optimal range: Gel strength should be adequate to suspend cuttings but not excessively high to cause operational challenges.
Electrical Stability (or Mud Resistivity) in Oil Muds:
- What it is: Electrical stability measures the ability of the drilling mud to resist electrical current, typically indicated by the Electrical Stability Test (EST).
- Why it is important:
- The electrical stability of mud provides an indication of its ability to withstand contamination and maintain its integrity during drilling.
- It helps detect changes in the mud properties caused by contamination.
- How to interpret it:
- High electrical stability: Indicates that the mud is resistant to contamination and has good structural integrity.
- Low electrical stability: May indicate that the mud is degrading, likely due to contamination or breakdown of the mud structure (emulsion).
Sand Content:
- What it is: Sand content refers to the amount of sand-like material present in the drilling mud, typically measured by screening the mud and measuring the volume of sand that remains. It is reported in percent
– Why it is important:
- What it is: Sand content refers to the amount of sand-like material present in the drilling mud, typically measured by screening the mud and measuring the volume of sand that remains. It is reported in percent
- High sand content can increase the viscosity of the mud, leading to poor hole cleaning, increased pump pressure, high erosion of pipes and equipment, and difficulty in controlling the mud properties.
- High sand content can also adversely affect the filtration properties of the mud.
- How to interpret it:
- High sand content: Indicates poor hole cleaning and higher risk of equipment wear.
- Low sand content: Ensures smooth mud flow and effective hole cleaning.
- Optimal range: Sand content should be kept minimal with solids equipment to prevent operational issues.
Conclusion:
Regular monitoring these mud properties ensures that the drilling operation is safe, efficient, and effective. Proper interpretation of these parameters helps operators make timely adjustments to the mud composition, thereby preventing wellbore instability, controlling well pressure, and ensuring effective hole cleaning. Regular testing and adjustments are required to account for changing well conditions, formation pressures, and operational challenges. Observing trends often enables the rig crew take preventive action before major problems endanger the operations.
For more information on Drilling Mud for Well Control, read my Well Control Manual, which may be purchased in the Catalogue section of this website at: Well Control Manual V2.6 by Edwin Ritchie
What is the minimum viscosity in water-based muds to suspend barite?
In water-based muds, the minimum viscosity required to effectively suspend barite (a weighted material used to increase the density of the drilling mud) depends on several factors, including the barite concentration, the mud density, and the drilling conditions (such as the depth of the well, the type of formations being drilled, and the flow rate of the mud).
However, general guidelines are provided based on the need to ensure the barite remains suspended in the mud when circulation stops and during periods of non-circulation, such as when the drill string is pulled out of the hole.
Minimum Viscosity for Suspending Barite:
Plastic Viscosity (PV): Typically, to suspend barite in water-based muds, the plastic viscosity should generally be at least 30-40 cP (centipoise), although this can vary depending on the amount of barite added and the mud formulation.
Higher viscosities are often required if a significant amount of barite is added to achieve the desired mud weight (density).If the barite content is very high (e.g., > 18-20 ppg), the plastic viscosity may need to be 50 cP or higher to suspend the particles effectively, especially in deep wells where higher mud weights are often necessary.
Yield Point (YP): The yield point, which is a measure of the mud’s ability to suspend cuttings, should ideally be at least 10-15 lb/100ft². Higher yield points can help suspend barite and prevent it from settling during non-circulation periods.
Why Viscosity is Important:
Barite Suspension: Barite particles are dense and have a tendency to settle out of the mud if the viscosity is too low. Maintaining adequate viscosity ensures that barite remains suspended in the mud, preventing the buildup of excess solids at the bottom of the well and helping maintain desired mud weight.
Hole Cleaning: A viscosity that’s too low not only prevents proper barite suspension but can also affect the ability of the mud to carry drill cuttings to the surface, which is crucial for preventing stuck pipe and other drilling problems.
Conclusion:
The minimum viscosity for suspending barite in water-based muds typically falls in the range of 30-40 cP for most applications. However, for high-density muds (with significant amounts of barite), the viscosity may need to be higher (up to 50 cP or more) to ensure proper suspension and prevent barite from settling during non-circulation periods. These values may vary depending on specific well conditions and operational requirements.
For more information on Drilling Mud for Well Control, read my Well Control Manual, which may be purchased in the Catalogue section of this website at: Well Control Manual V2.6 by Edwin Ritchie
Hydrostatic Pressure and Its Role in Well Control
Hydrostatic pressure refers to the pressure exerted by a column of fluid due to the weight of the
fluid itself. In the context of drilling operations, this pressure is generated by the drilling mud
(also known as drilling fluid) inside the wellbore. Hydrostatic pressure is a crucial concept in
well control because it helps to balance and regulate the pressure within the well, preventing
dangerous situations such as blowouts.
How Hydrostatic Pressure is Calculated
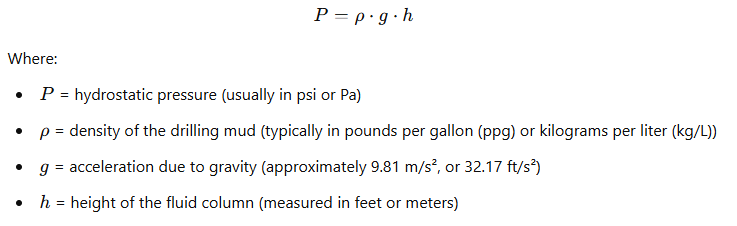
The hydrostatic pressure in a well is calculated using the following formula:
In simpler terms, hydrostatic pressure is directly proportional to the mud weight and the height
of the mud column in the wellbore. The deeper the well and the heavier the mud, the greater the
hydrostatic pressure.
Hydrostatic Pressure and Well Control
Hydrostatic pressure plays a critical role in controlling the well during drilling operations,
particularly for the following reasons:
the rock formations being drilled. As drilling progresses, the pressure exerted by
the formation fluids must be counteracted by the hydrostatic pressure of the
drilling mud to maintain well control.
o If the hydrostatic pressure is too low compared to the formation pressure,
formation fluids (oil, gas, or water) may flow into the wellbore, a phenomenon
known as a kick. If uncontrolled, this can lead to a blowout.
o If the hydrostatic pressure is too high, it can lead to formation fracturing. In this
case, the mud can penetrate the formation, potentially causing the wellbore to
become unstable and resulting in loss of circulation or other complications.
hydrostatic pressure. This can happen when the drilling mud is not dense enough
to counterbalance the formation pressure.
o Once a kick occurs, it is essential to respond quickly by shutting in the well and
using well control techniques (such as circulating out the influx of fluids) to
prevent a blowout.
o A blowout is a sudden and uncontrolled release of formation fluids from the
wellbore to the surface. It typically happens when the well is not adequately
controlled and the hydrostatic pressure is unable to counteract the formation
pressure.
uncontrolled fluid influx and helping to maintain well integrity. The pressure
exerted by the mud column keeps the well sealed, preventing gas or oil from
migrating into the wellbore.
o Monitoring and adjusting hydrostatic pressure is essential to ensure the well
remains in balance with formation pressures.
Factors That Affect Hydrostatic Pressure in Well Control:
o The weight of the drilling mud is the primary factor influencing hydrostatic
pressure. By adjusting the mud weight (increasing or decreasing the density of
the drilling fluid), the hydrostatic pressure can be modified.
o In deep wells or high-pressure zones, the mud weight is typically increased to
counteract high formation pressures. In shallow wells or low-pressure formations,
the mud weight may be reduced to avoid fracturing the formation.
in turn increases the hydrostatic pressure. The deeper the well, the higher the
hydrostatic pressure required to balance formation pressure.
o In deepwater drilling or ultra-deep wells, managing hydrostatic pressure is
particularly challenging due to the vast depth and high formation pressures
encountered.
hydrostatic pressure. For example, in an offshore rig, where the water depth adds
to the total height of the mud column, the total hydrostatic pressure must account
for both the height of the water column and the mud column.
In Summary:
Hydrostatic pressure is the pressure exerted by a column of drilling mud in the wellbore and is
crucial for maintaining well control during drilling operations. It acts as a counterbalance to
formation pressures, preventing the influx of formation fluids into the well (a kick) or the loss of
mud to the formation (fracturing). Proper management and monitoring of hydrostatic pressure
are essential to avoid dangerous well control issues like blowouts. Adjusting the mud weight and
considering well depth are the primary ways to control and optimize hydrostatic pressure for safe
and efficient drilling operations.
For more information on Drilling Mud for Well Control, read my Well Control Manual, which may be purchased in the Catalogue section of this website at: Well Control Manual V2.6 by Edwin Ritchie
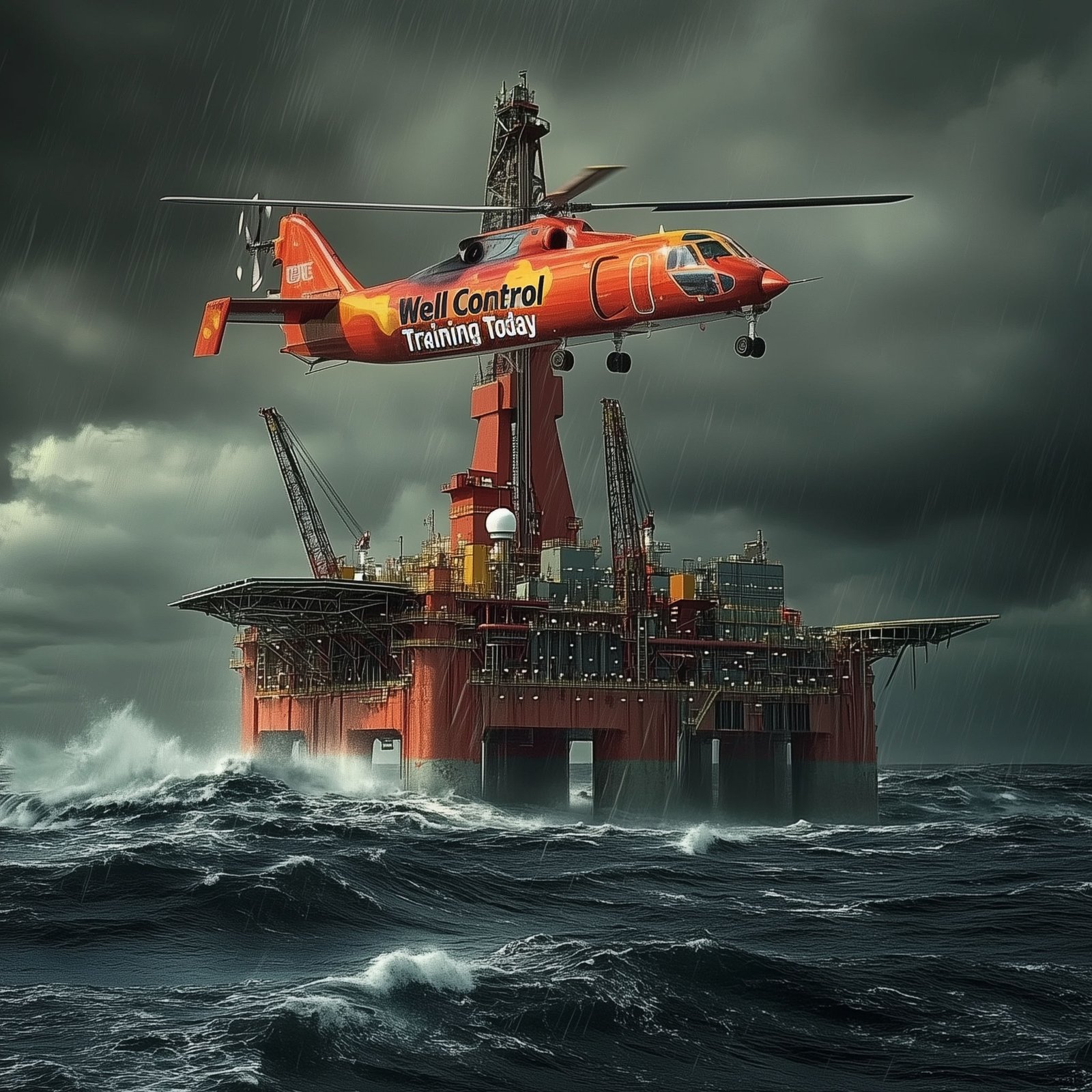